Additive Manufacturingを知る
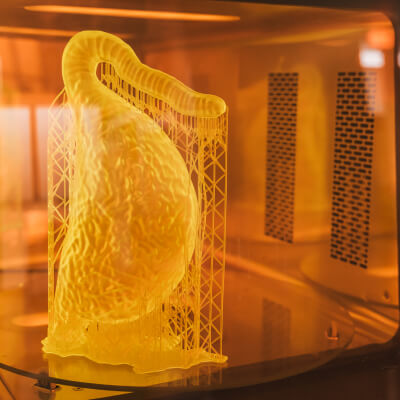
AMスタートガイド
基礎知識と実践のポイント
AMはさまざまな技術が複雑に絡み合っています。そこで、AMをより理解していただくために、役立つ知識を「AMとは」「造形方式」「3Dデータの作成」という3つのカテゴリに分け、わかりやすく整理しました。
AMとは
3Dデータをもとに、素材を一層ずつ積み重ねて形状を作り出す加算型製造技術です。
「Additive Manufacturing(AM)」は、一般に3Dプリントと呼ばれる技術を指し、3DCADなどで作成された3Dデータをもとに、素材を一層ずつ積み重ねて形状を作り出す製造技術です。
従来の「除去加工」(素材を削り出して形状を作る方法)や「塑性加工」(素材を型に押し込んで変形させる方法)と比較して、形状設計の自由度が高く、従来の技術では難しかった複雑な形状の製造が可能となります。
近年では、試作用途だけでなく、本格的な製造技術としてもAMの活用が進んでおり、今後さらに主要な製造技術の一つとして広がることが期待されています。
01
試作技術から製造技術へ:
Rapid PrototypingからAdditive Manufacturingへ
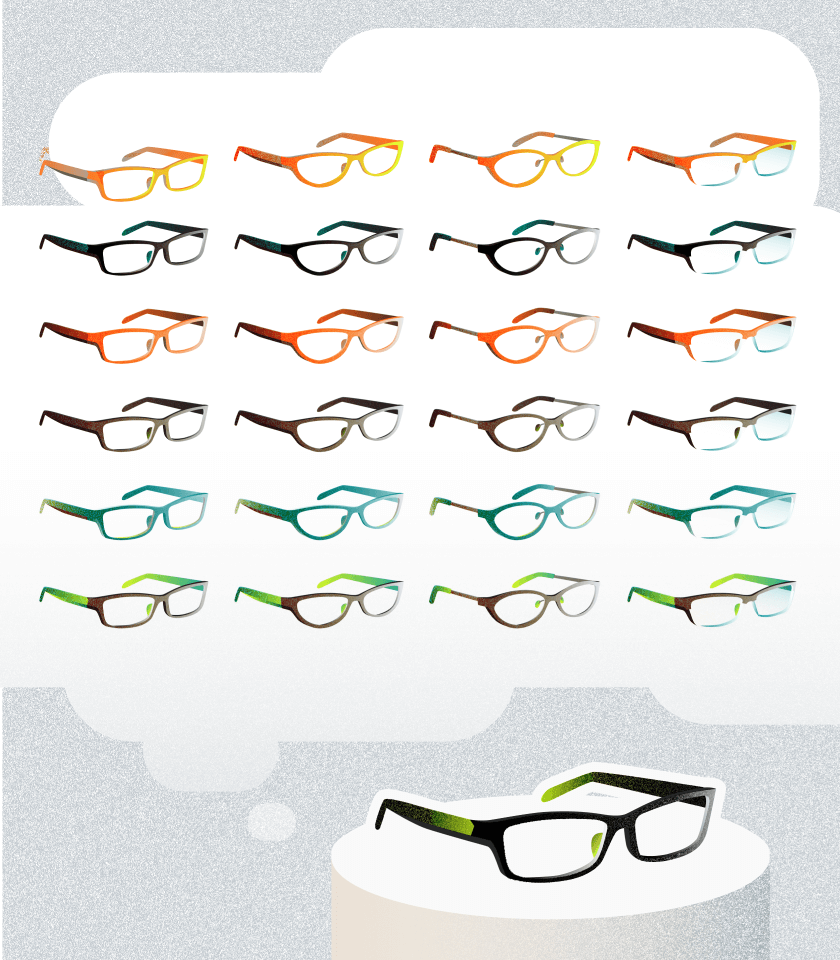
3Dプリント技術は、もともと「Rapid Prototyping」として知られていました。名前の通り、試作を迅速に行える技術として評価され、主に製造業の現場で広まりました。当時の3Dプリンターは技術的に未成熟で、高品質な材料が使えず、精度にも限界があったため、試作用途に限られた技術と考えられていたのです。
しかし、近年では3Dプリント技術を「試作」だけでなく「製造」でも活用する動きが広がっています。これには、製品の企画・設計段階から3Dプリントを前提に取り入れる「Design for AM」(AMのためのデザイン)という新たな考え方が普及していることが大きく影響しています。この設計アプローチにより、従来の生産技術では難しかった製品開発が可能となり、世界中で3Dプリントを活用した製造事例が急増しています。
3Dプリント技術は、黎明期の「Rapid Prototyping」から、今や「Additive Manufacturing」として新たな製造技術の普及期を迎えています。
02
Additive Manufacturingの可能性
Additive Manufacturing(AM)の可能性は、「従来は難しかった形状の加工が可能になり、形状の最適化が進むことでコスト削減に繋がる」といった点で語られることが多いです。しかし、AMは単に既存の製造プロセスを改善するツールにとどまらず、製品の開発・生産・流通のプロセス全体を根本的に変革し、ものづくりに革命を起こす技術です。
ここでは、AMの可能性の一部をご紹介します。
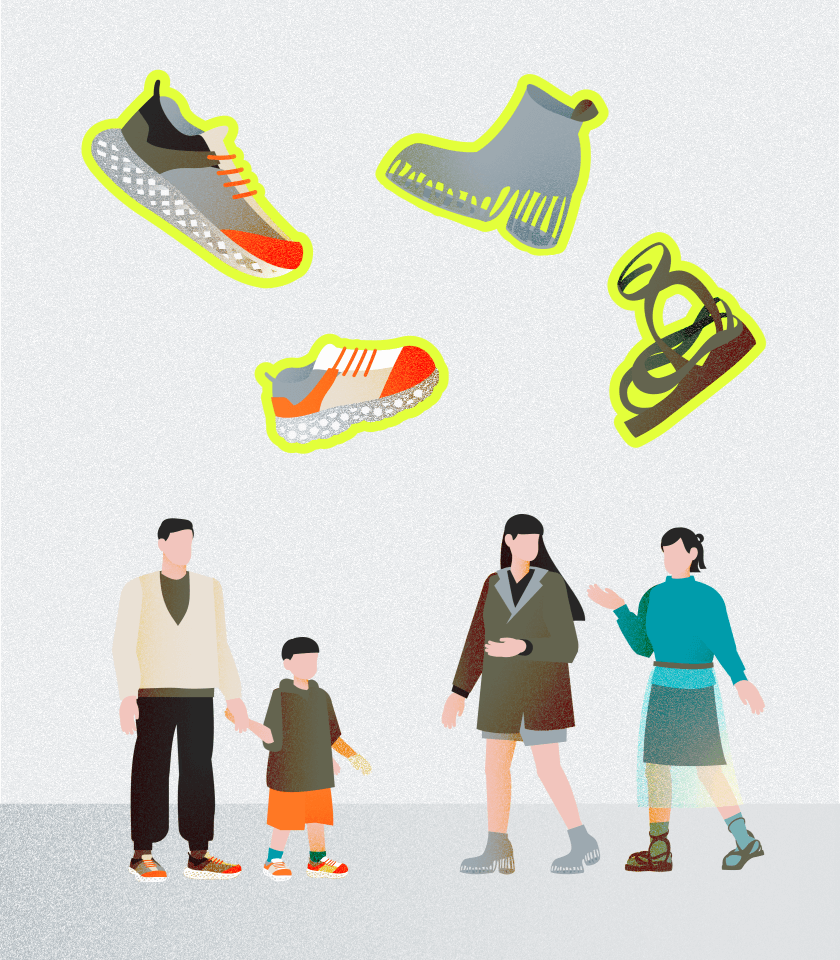
カスタマイズ生産の実現
Additive Manufacturing(AM)は、個々に異なる形状でも追加コストをかけずに生産できる技術です。たとえば、1人ひとりに合わせたパーソナライズされたフットウェアなどを、従来よりも低コストで製造可能です。多様化する価値観に応える「超多品種・超少量生産」を実現する、次世代の製造技術です。
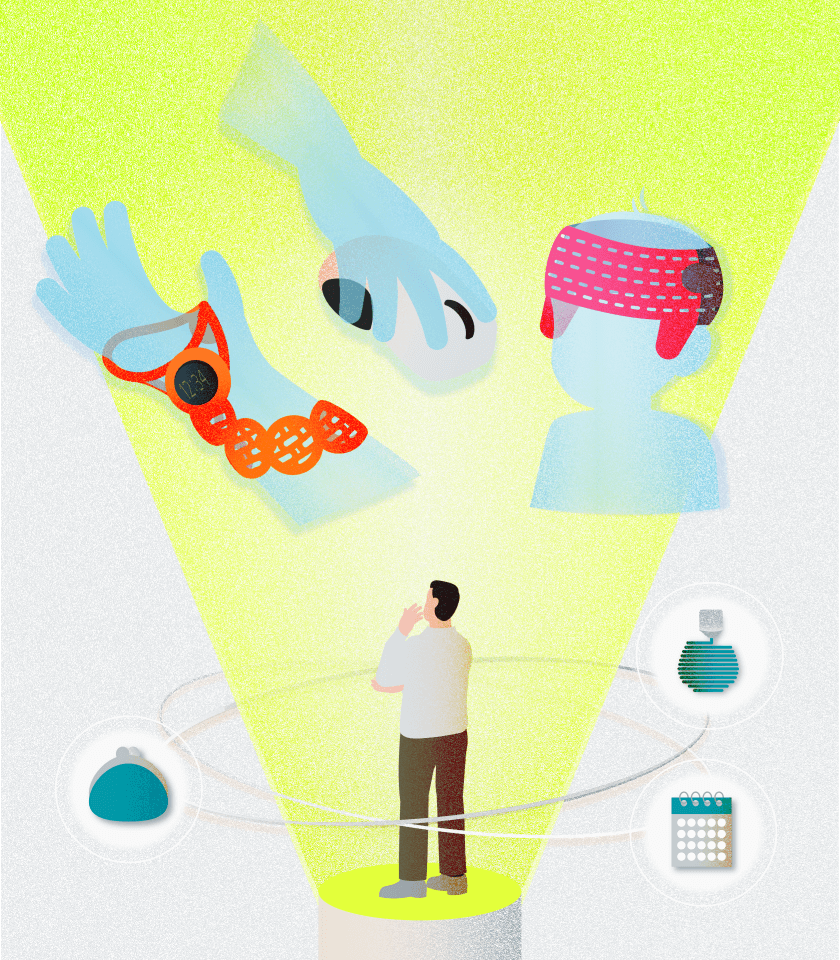
製品化の可能性を広げる技術
Additive Manufacturing(AM)は、形状の自由度が高く、低コストかつ短期間で単品生産が可能な技術です。この特性により、従来では難しかった製品を低コストでオンデマンド生産できるようになりました。AMを前提に製品企画・開発を行うことで、形状や生産ロットの制約を緩和し、これまで実現できなかった製品アイデアも検討・設計可能になります。 これにより、技術的・コスト的な制約で市場投入を諦めていた製品アイデアの実現が広がる可能性があります。
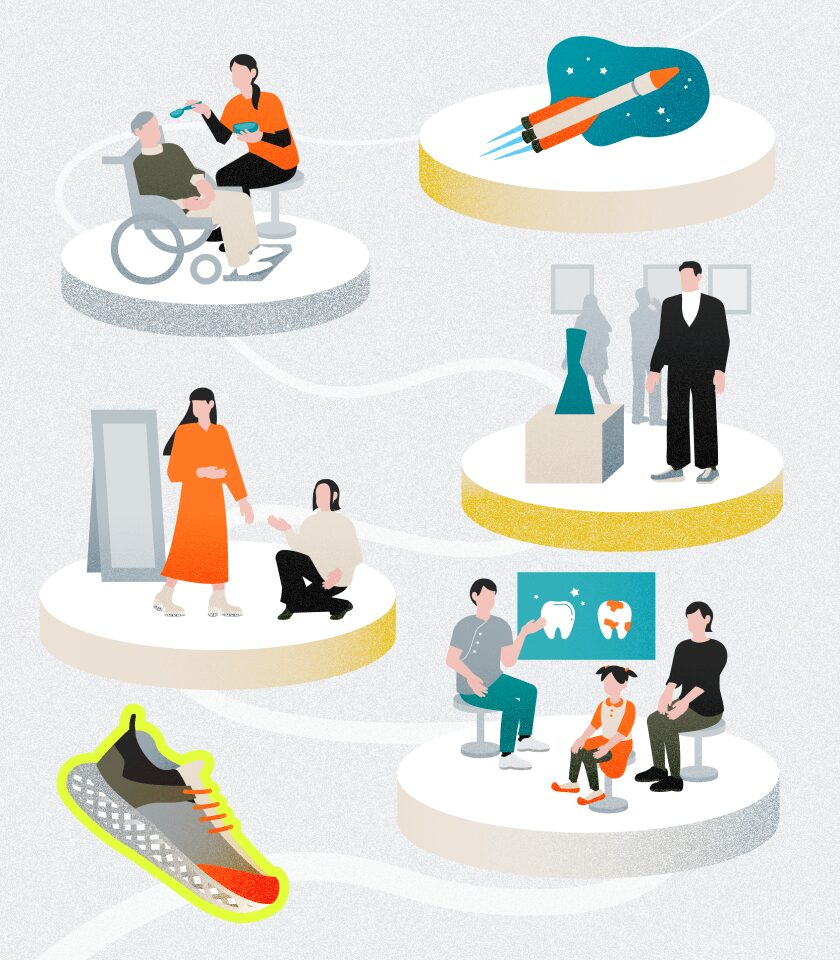
広がり続ける可能性
Additive Manufacturing(AM)や3Dプリンターという言葉は、単に加工方法の概念を指しているに過ぎません。実際には、多様な造形方式や材料が存在しています。
AMは比較的新しい技術であり、技術革新が急速に進展しています。新しい造形技術、材料、機械、関連ソフトウェアが次々と登場しており、AMの可能性は日々拡大しています。運用面での進化も進んでおり、今後、さまざまな分野での活用がさらに加速すると期待されています。
関連記事:進化するAM技術とその応用
Additive Manufacturing(AM)の基本概念から、主要な技術と材料の解説まで、AMをはじめて学ぶ方に役立つ情報を提供します。
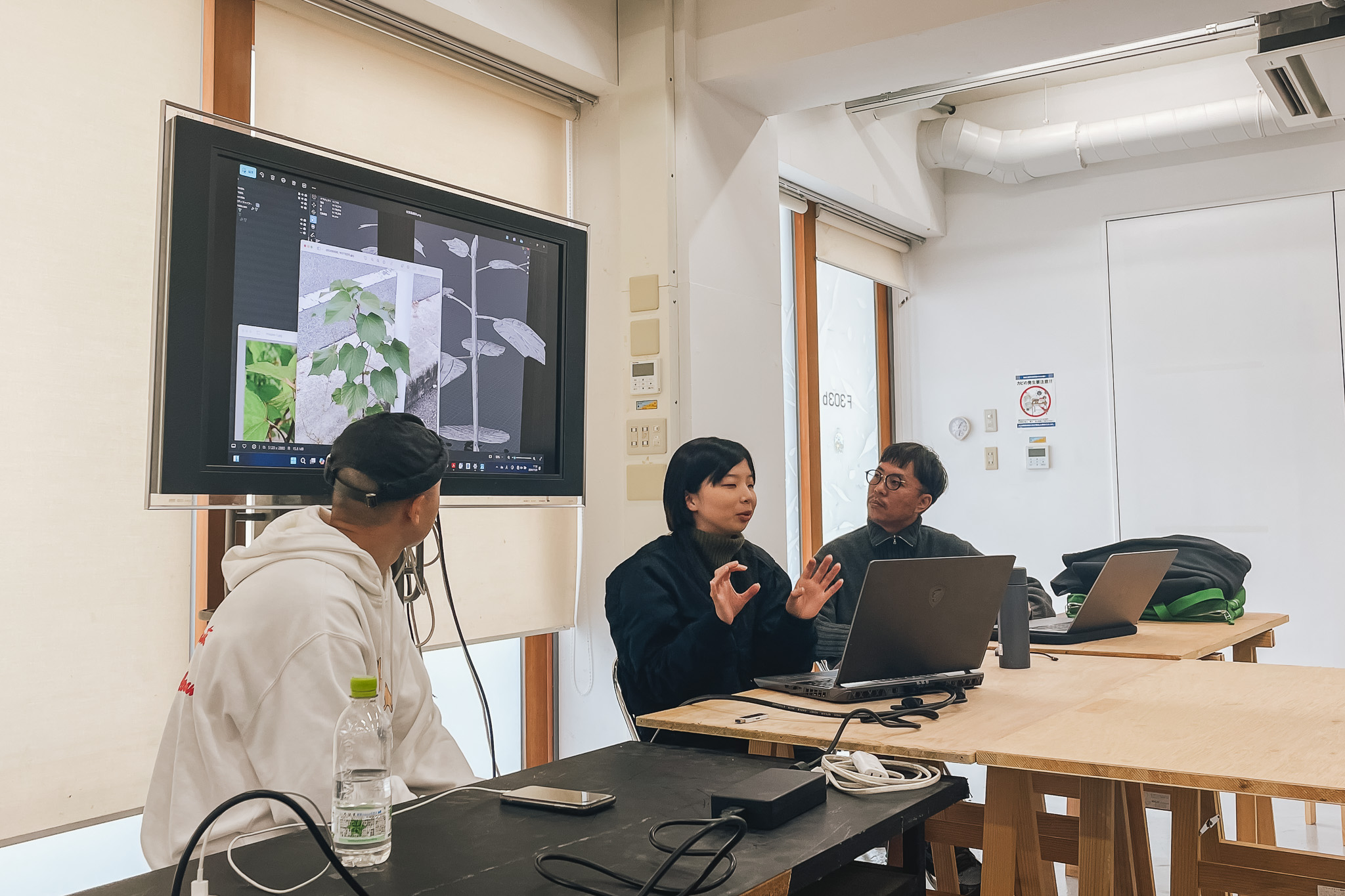
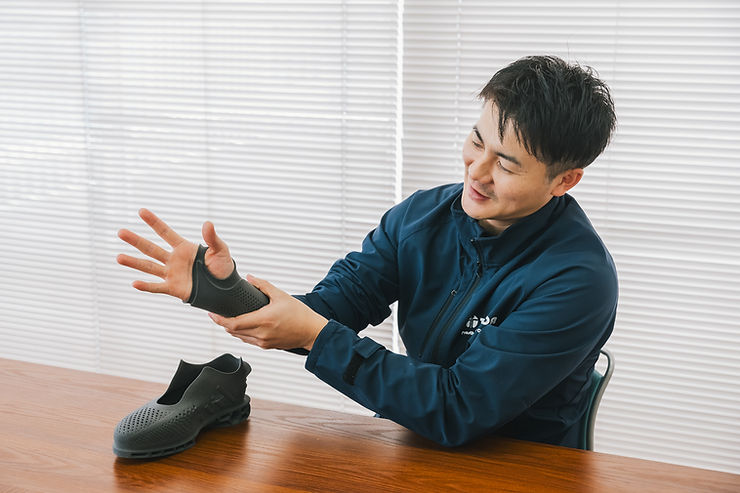
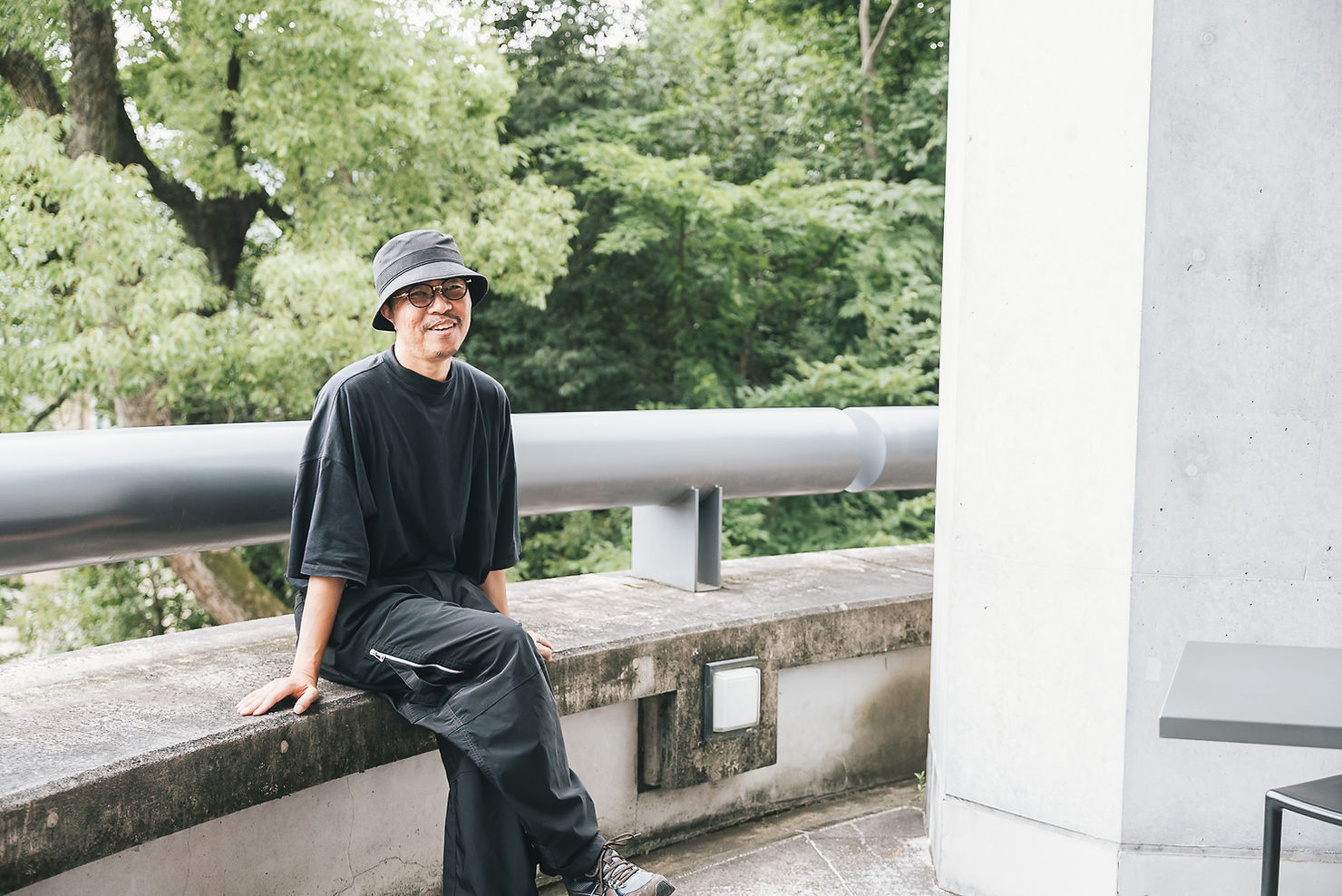
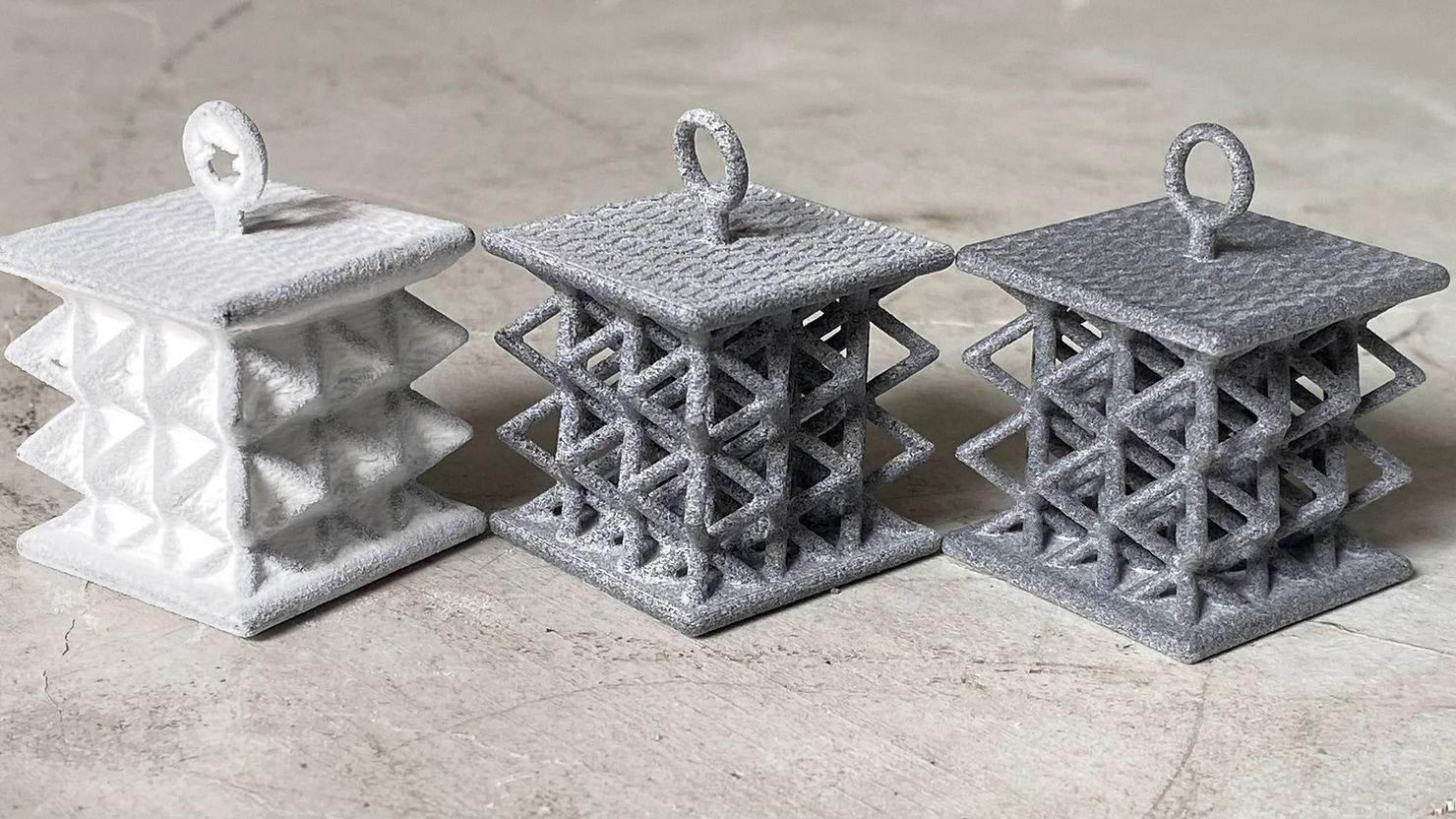
造形方式について
代表的な3Dプリンティングの造形方式を解説
Additive Manufacturing(以下AM)技術の中でも特に利用されている主要な造形方式について、その仕組みを詳しく紹介します。
01
材料押出法(Material Extrusion: MEX)
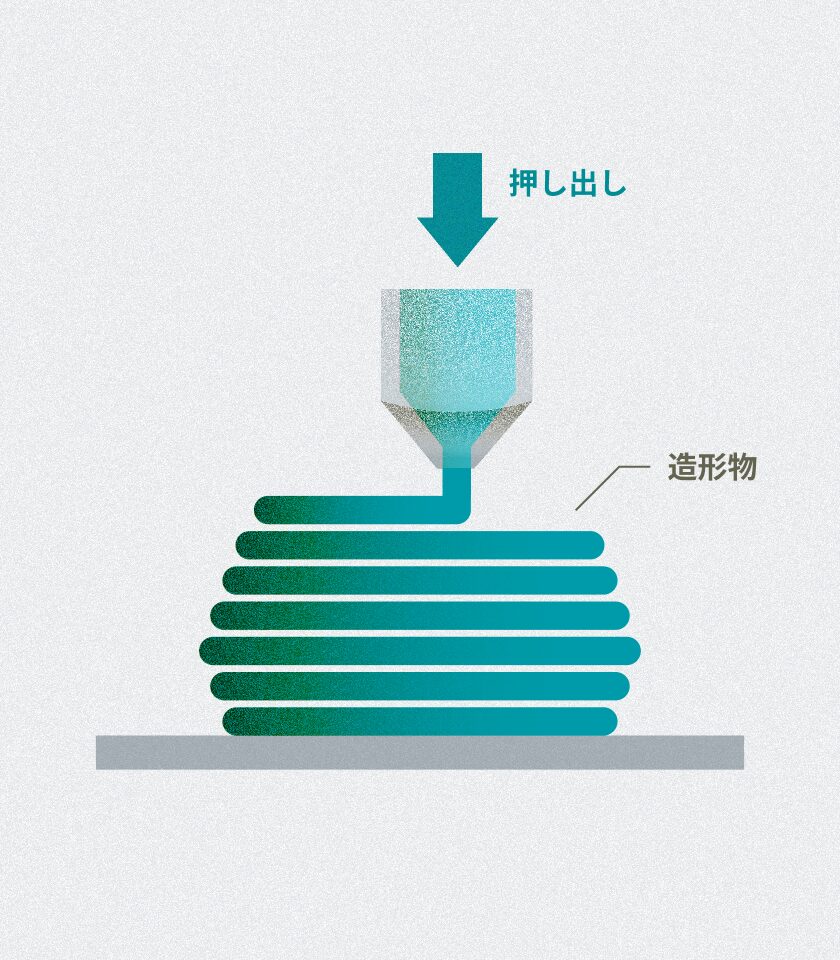
材料を吐出口へと押し出し、積層していく方式。熱で樹脂を溶かすため、熱可塑性樹脂を用いる。MEX方式は最もメジャーであるフィラメントを使用するFFF(Fused Filament Fabrication)と、ペレットを使用するFGF(Fused Granular Fabrication)など材料の形状によって大きく2つに分類される。
※広く知られている「FDM」は米・ストラタシス社の商標であり、本造形方式と同様の意味合いで使用される。
02
液槽光重合法(Vat Photopolymerization: VPP)
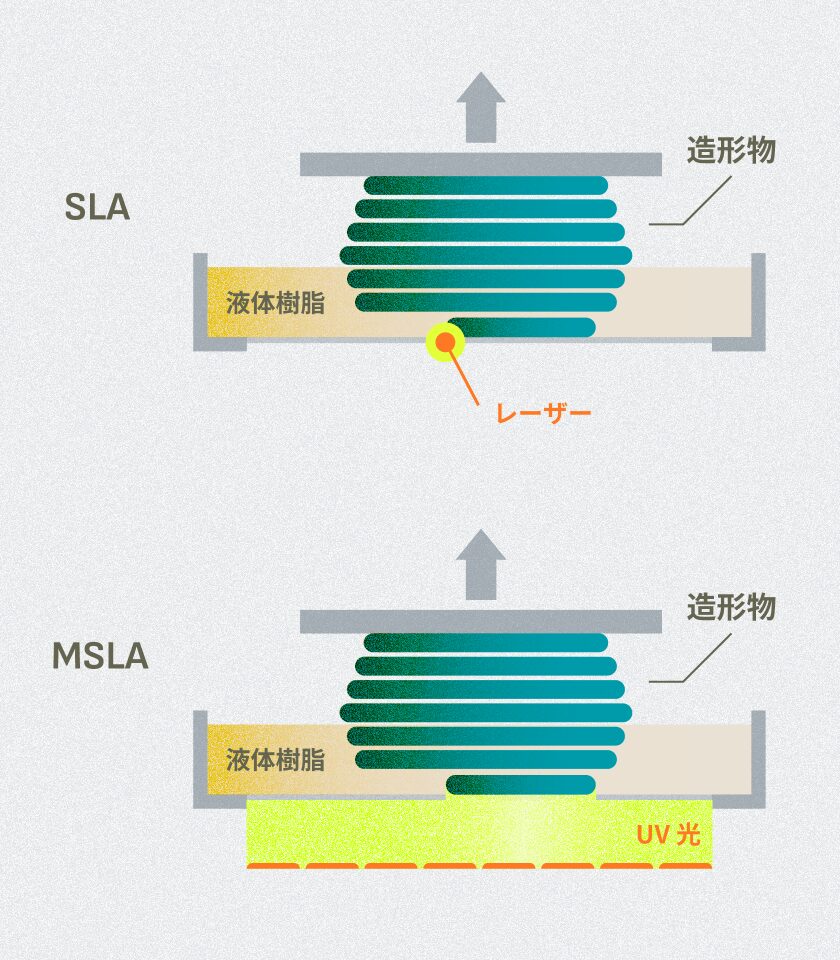
光硬化樹脂に光を当て、硬化させて積層していく方式。材料として紫外線で硬化するアクリル系・ウレタン系樹脂が挙げられる。3Dプリンタの製造方式の中でも光造形の歴史は最も古く、材料のバラエティは他の造形方式よりも豊かである。VPPにはレーザーを使用するSLA(Stereolithography)、プロジェクターを使用するDLP(Digital Light Processing)、UV光とLCDパネルを使用するMSLA(Masked Stereolithography / LCD)など光源の種類によって更に分類される。 また、造形物を吊り下げるように造形する規制液面法とレジン液に沈めるように造形する自由液面法があり、造形物の大きさなどに影響する。
03
粉末床溶融結合法(Powder Bed Fusion: PBF)
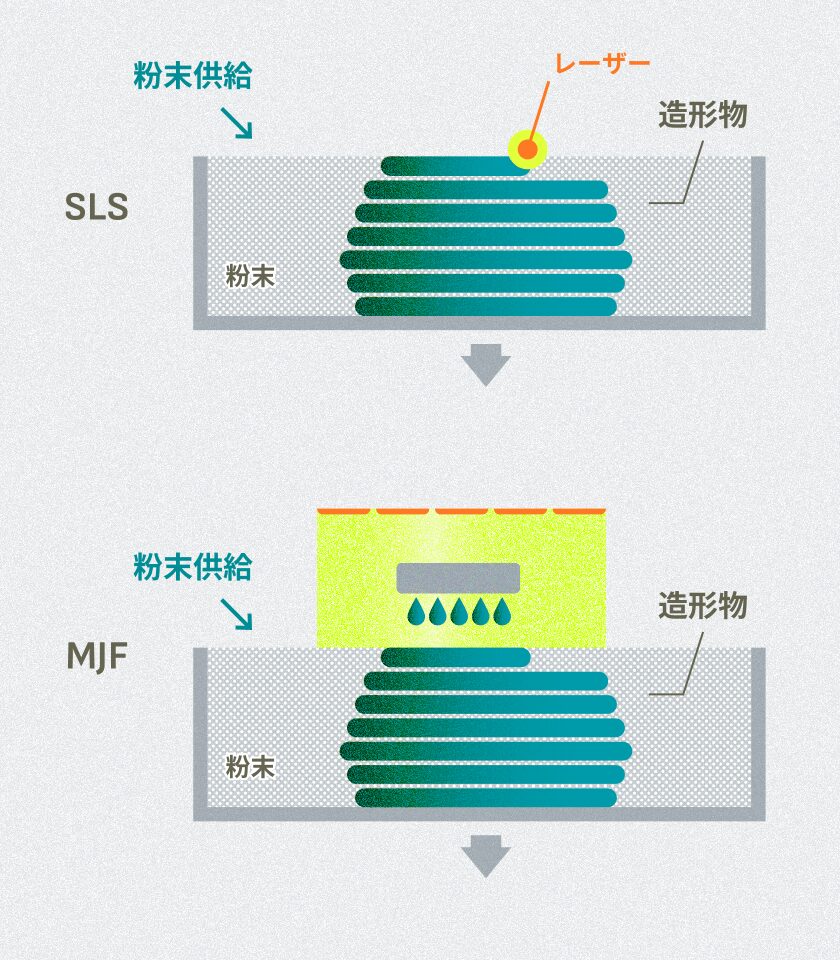
粉末状の材料を造形面全体に充填し、部分的に溶融させ積層していく方式。代表的な材料はポリアミド(ナイロン)で、現在ではポリプロピレン、TPUなども扱える。レーザーを熱源とし材料を焼結するSLS(Selected Laser Sintering)と薬剤と熱で溶融するMJF(Multi Jet Fusion)の2つに分類される。サポート材が不要であり、廃棄される部分が少ない点など、他方式と比較して量産性に優れている。
層同士の接合は、レーザー照射による溶融・焼結、である。
04
材料噴射法(Material Jetting: MJT)
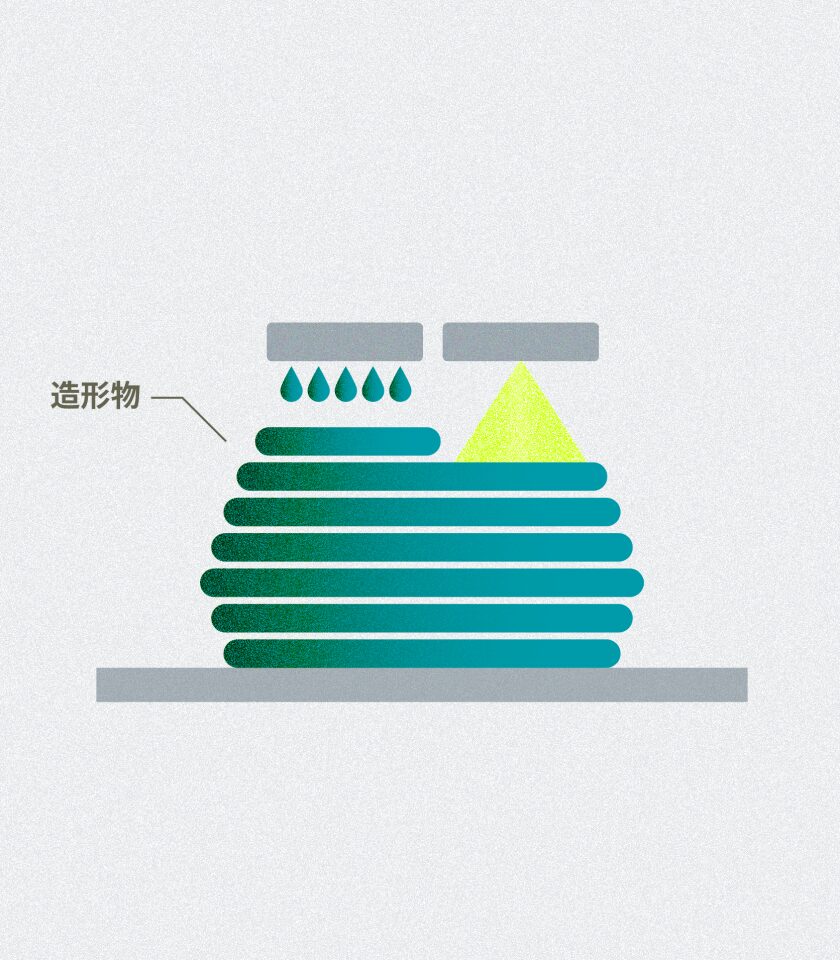
インクジェットノズルから材料(液滴)を選択的に吐出することで積層する。材料として、光硬化性樹脂やワックスなどが挙げられる。サポート材とモデルを別の材料とする機種が多い。着色した材料を同じ位置に吐出し、混ぜ合わせることでフルカラー化が可能。異なる物性の材料を混ぜ合わせることもできる。
層同士の接合は、化学結合、接着などである。
3Dデータ作成について
Additive Manufacturing(AM)に適した3Dデータの作成を解説します
Additive Manufacturing(AM)で高品質な造形を実現するためには、正確で適切な3Dデータの作成が重要です。ここでは、AMに最適な3Dデータを作成するためのポイントを解説します。モデリングソフトの選び方から、造形時に注意すべきデータの最適化手法、メッシュの精度やサポート構造の設計方法まで、具体的なステップを詳しく紹介します。
01
3Dモデルデータを作成する
3Dプリンティングにおいては、まず出力するための3Dデータが必要です。3Dデータを作成するために3DCADソフトを用いてモデリングをします。モデリングは大別すると3種類ありそれぞれに特徴があります。
ポリゴンモデリング
面及び立体を構成する頂点を定義していくモデリングです。
フィギュア制作など自由な形状を作成しやすい。
[例 Blender]
サーフェスモデリング
厚みの無い面を定義していくモデリングです。
家電の筐体や自動車のボディなど、自由曲面が多い形状を作成しやすい。
[例 Rhinoceros]
ソリッドモデリング
中身の詰まった立体を定義していくモデリングです。
メカ設計など複数のパーツからなるモデルデータの作成しやすい。
質量や体積の計算が可能で実物に近いシミュレーションも可能。
[例 Fusion360, SolidWorks]
これらのどの方法でも3Dプリンタで出力するためのモデルを制作することができます。また、これらの手法を1つの3DCADソフト内で組み合わせて形状を作成していくこともあります。ただし、1と2のモデリング方法では面や頂点を定義して形状を作っていくので、現実に存在することができない形状もデータとして成り立ってしまいます。
例えばポリゴンモデリングでコップを作ってみるとします。
一見すると普通のコップに見えます。
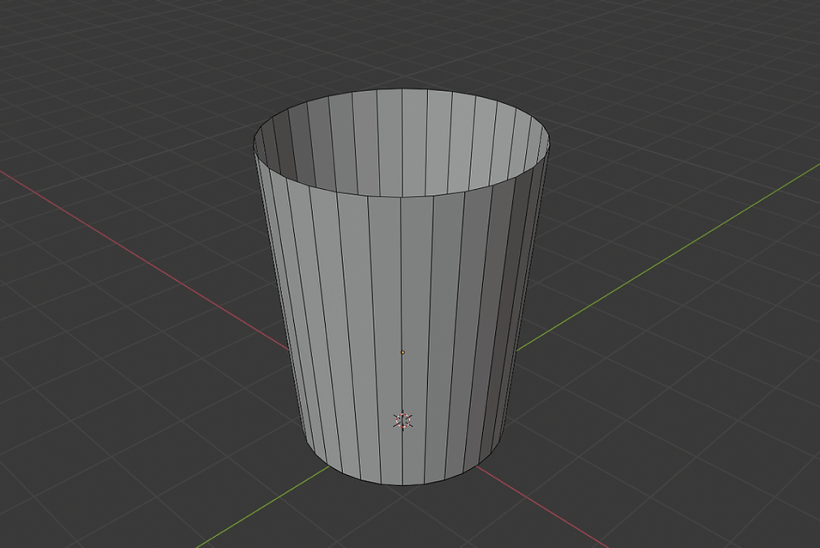
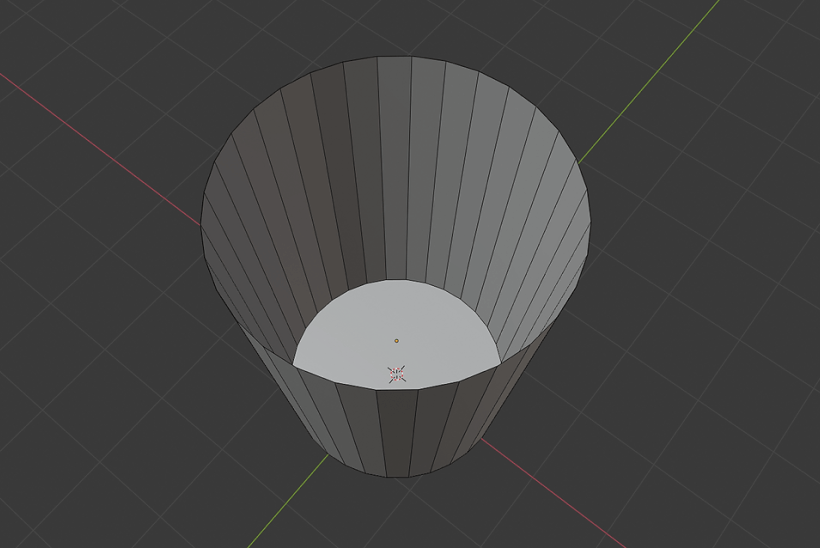
しかし、よく見るとコップの底と壁には厚みがありません。ソフトウェア上ではコップのように見えますが、実在しない形状です。『閉じられていないモデル』と呼ばれることがあります。こうなると3Dプリンタでは出力することはできません。
正しくは以下のように厚みを与える必要があります。
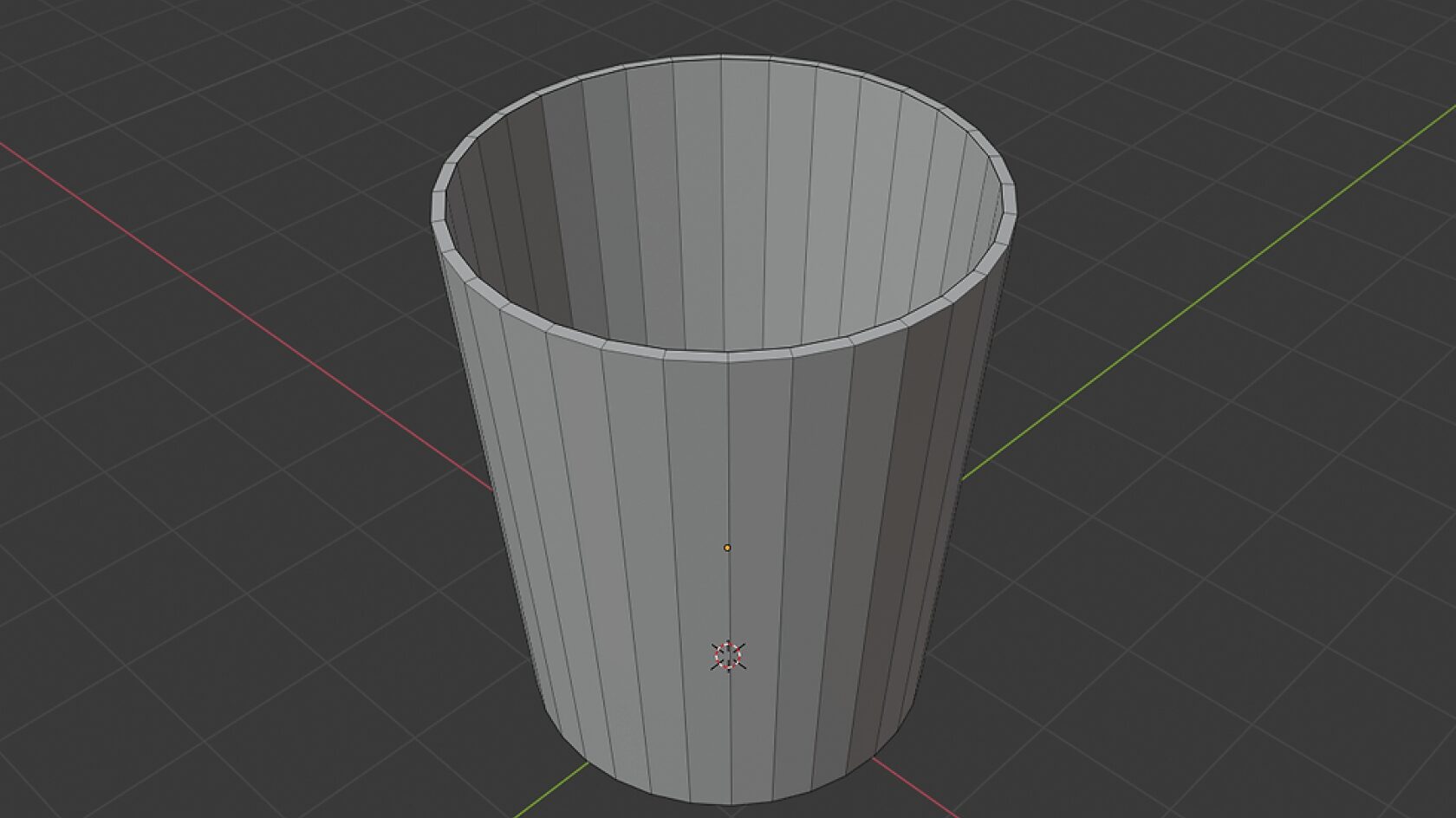
このように、ポリゴンモデリングとサーフェスモデリングでは厚みの無い形状でもデータとして成り立つので注意が必要です。
一方でソリッドモデリングでは作成した形状には必ず体積があるので、実在しないような形状になることはありません。すべて『閉じられたモデル』というわけです。
だからといって3Dプリントするにはソリッドモデリングでないといけないということはありません。形状の作り方に違いがあるだけです。(言い換えると作りたい形状によってはモデリング方法を使い分けていく必要があり、3Dプリントに使うデータを作る際には上記のようなことを念頭においておけば何も問題はありません。)
さて、これらとは別にモデリングの進め方として、パラメトリックモデリングという手法があります。これはモデリングの種類というよりは設計思想に近いものです。
例えば、上述のようにコップを作成する際にはコップの高さ、壁の厚さ、飲み口の直径、底の直径など、1度3Dプリントしてみて実際に手に取ってみて、これらの寸法を調整したり、一度に複数のパターンの形状を3Dプリントして検討したりすることがあるでしょう。
コップのような簡単な形状の場合はいくつもモデリングすれば済むかもしれませんが、これが複雑な形状になってくると、検討したい箇所の寸法やパーツが多くなり、それぞれ手作業でモデリングをするのは大変な作業になってしまいます。
そこで、あらかじめ検討したい寸法やパーツの個数などを決めて、それらの値を後から変更していくことで多くのパターンのモデルを容易に作成することをできるようにするのがパラメトリックモデリングです。このパラメトリックモデリングにおいて現在様々な分野で使用されているのがRhinocerosとGrasshopperです。
下の画像はファンの形状をRhinocerosとGrasshopperを用いてパラメトリックモデリングで生成した様子です。ファンの直径や羽の枚数、形状などをスライダーを動かすだけで変更できます。
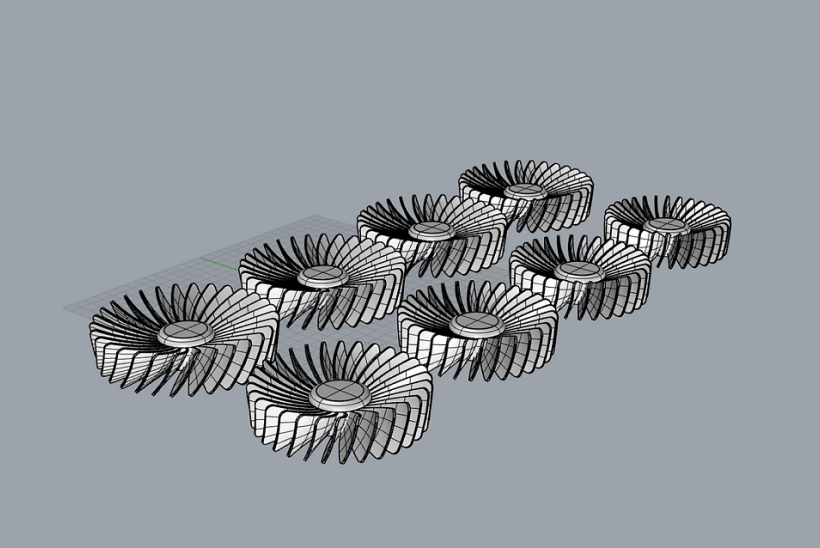
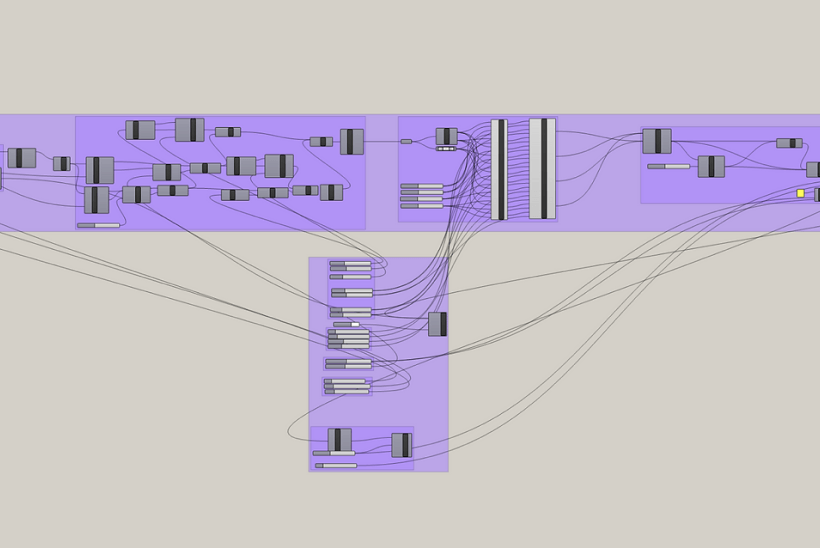
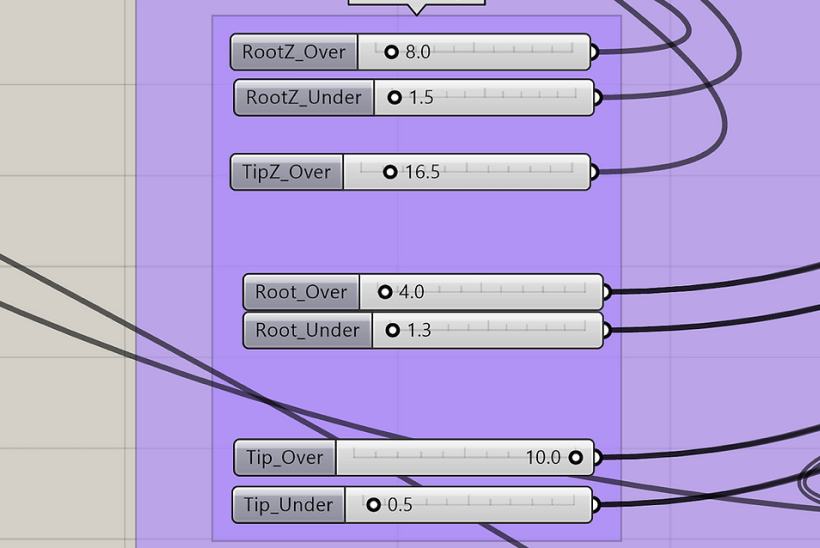
grasshopperではノードを用いてプログラミングを行います。アルゴリズムで形状を作成していくのでアルゴリズム内の変数をスライダーを使って変更することで形状を自由自在に操ることができます。
02
3Dモデルデータを3Dプリント用に変換する
現在、3Dプリント用のデータとしてもっとも一般的な形式がSTLとOBJ形式です。
基本的に3Dプリンタで出力する際はこのどちらかの形式のデータがあれば出力できないということは無いでしょう。

3Dモデリングソフトでデータを作っている際、そのデータはソフトウェア独自の形式です。例えばblenderですと.blendファイルです。Rhinocerosだと.3dmファイルです。
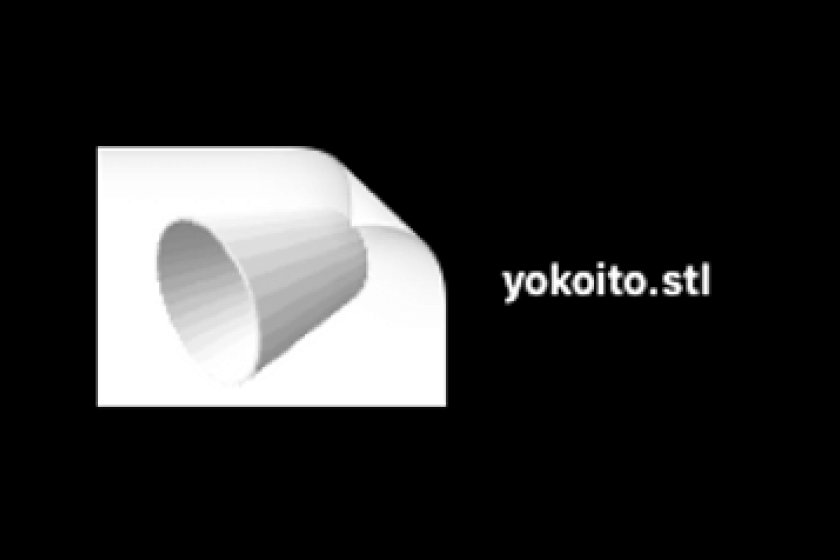
これらのデータも3Dデータなのですが、3Dプリント用にデータを変換する必要があります。これはほとんどのモデリングソフト内で可能です。例えばblenderでモデルデータを作っている場合はblender内からSTLまたはOBJに変換して書き出すことができます。
STLとOBJではどんな違いがあるのでしょうか?
- STL:ポリゴンメッシュ(三角)、色情報なし
- OBJ:ポリゴンメッシュ(四角)、色情報あり
OBJファイルは3Dプリントだけでなく、3DCGの業界でもよく使われているのでモデルに色情報持たせることができますが、ほとんど場合3Dプリントする素材の色は3Dプリンタで使う素材に依存するのでフルカラー出力が可能な特殊な3Dプリンタを使う場合を除くと色情報は必要ありません。なのでほとんどの場合STLにしておけば問題ありません。
また、どちらの形式もポリゴンメッシュ形式となります。これはどういうことかというと、形状はすべて頂点により定義されているということです。
球体のモデルをFusion360で作成してみましょう。
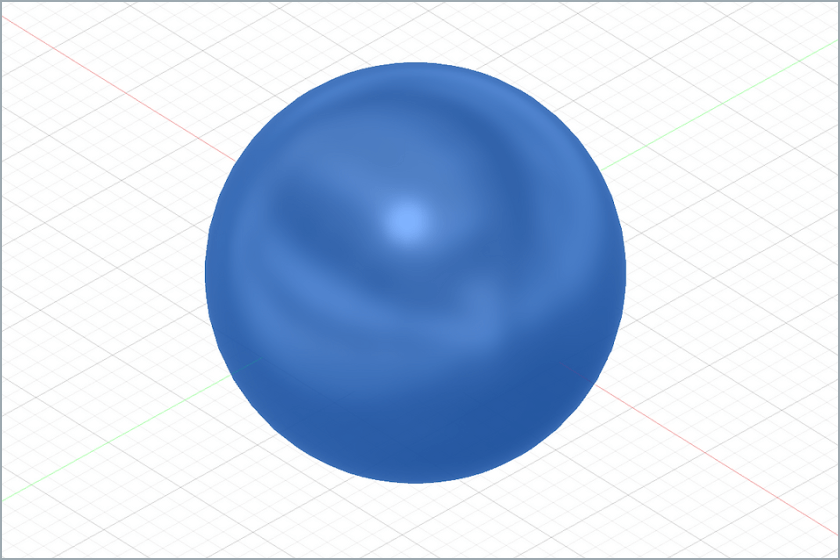
球体の表面はツルッとしています。これは完全な球体であり、ポリゴンメッシュではありません。それではSTLにしてみます。
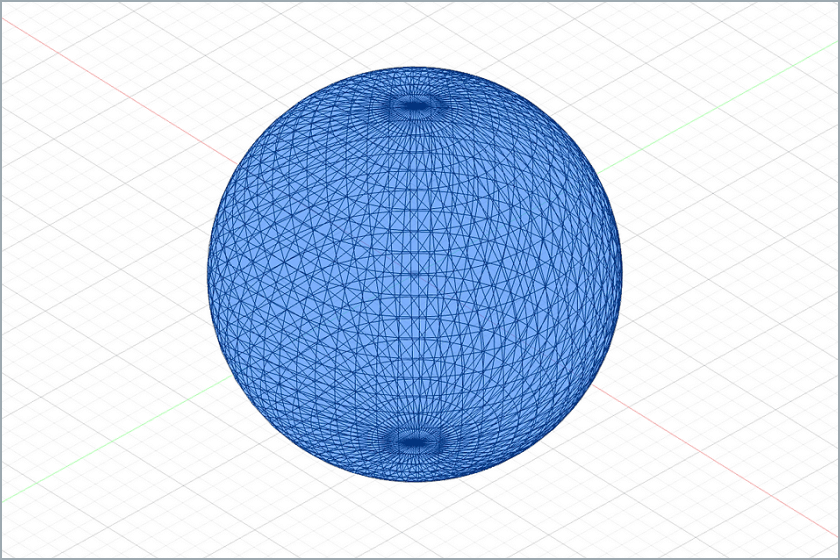
一見綺麗な球に見えますが、寄ると3角形の平面だけで構成されていることがわかります。
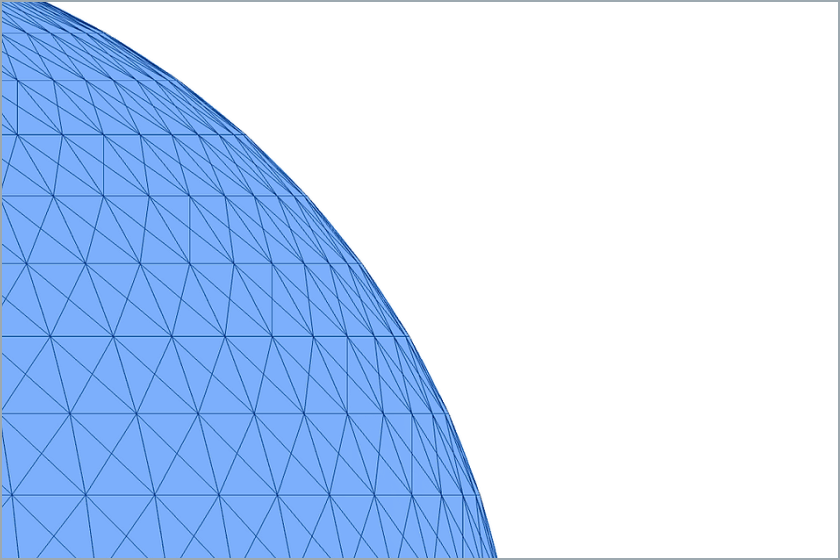
書き出しの際にこのメッシュをどれだけ細かくするかは設定することができます。もちろん細かくすれば綺麗な球体に近づきますが頂点の情報が増えるのでデータは重くなってしまうので注意が必要です。STLに変換した状態で1度モデルデータを確認しておくのも大切です。
03
プリンタ用の制御ファイルを生成する
3Dプリンタはモデルデータだけで動かすことはできません。
モデリングソフトから書き出したSTLまたはOBJファイルを使って3Dプリンタを制御するためのファイルを生成する必要があります。このプリンタ用のソフトウェアは一般的にスライサーと呼ばれます。AMでは材料を積層して造形していくので、スライサーを使ってモデルデータを文字通りスライスする必要があります。
このスライサーの設定が最終的に3Dプリンタから出力される形状を決定します。ソフトによっては膨大な設定項目があります。中でも最も仕上がりに影響するのは材料の積層ピッチです。
FDMプリンタ用のスライサーであるCuraを使ってモデルをスライスしてみましょう。
積層ピッチ0.1mmと0.3mmの比較です。
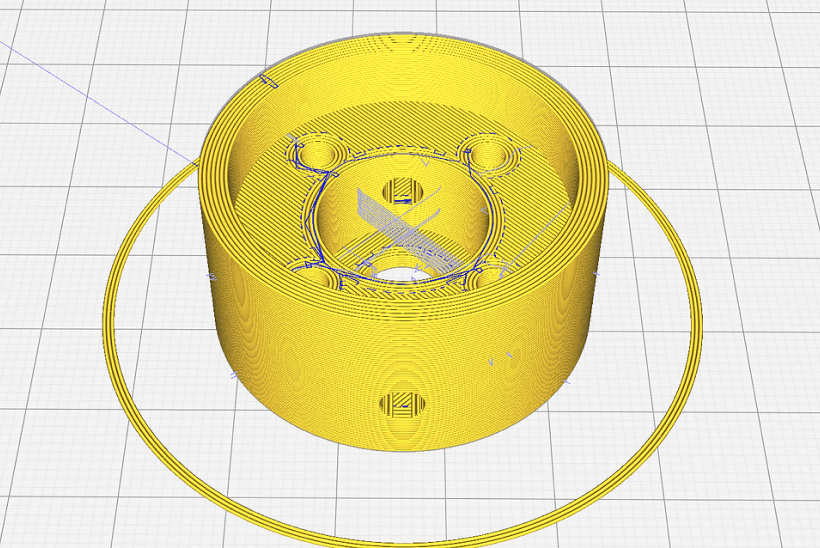
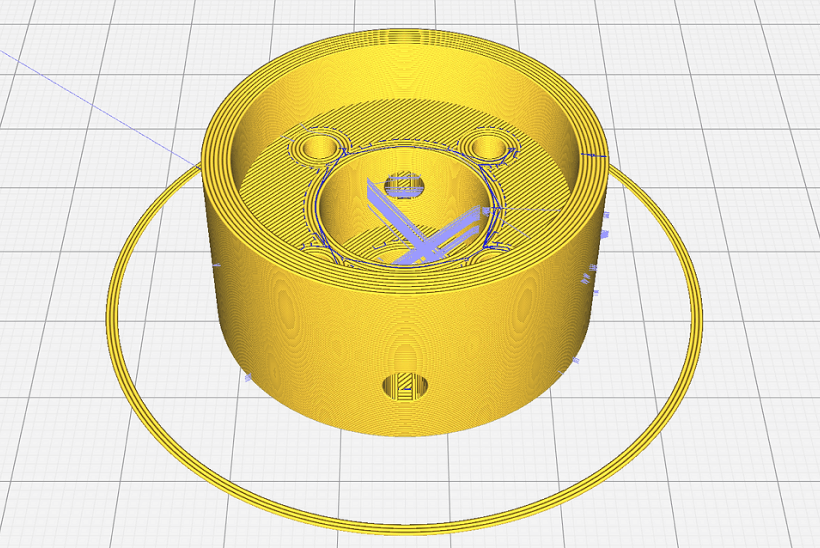
上から見るとあまり違いがわかりませんが、積層方向に着目すると穴の形が積層ピッチによって大きく影響されているのがわかります。
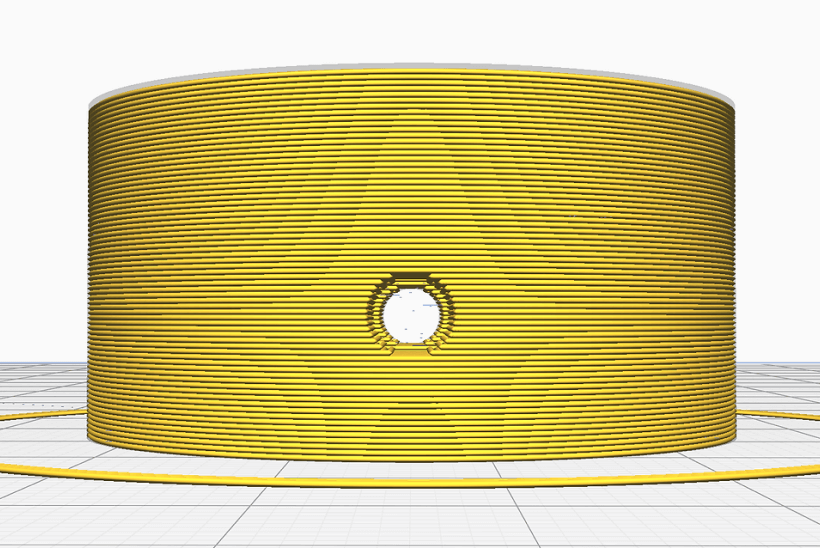
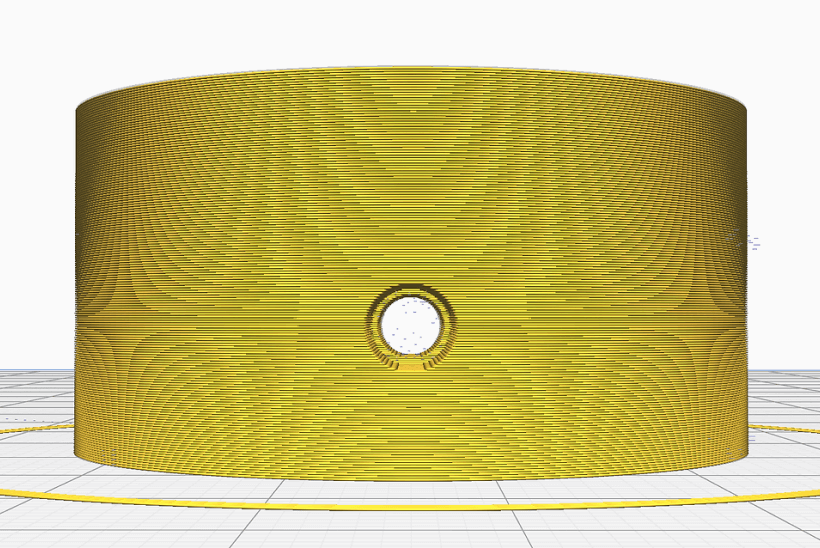
以上のように3Dモデルデータの作成から3Dプリント出力までは手順があります。
現段階の技術では3Dモデルデータがあればそのままそれが現実の物として出力されるようなことはありません。しかし、AMという造形方法を理解し設計段階からそれを念頭に置いてデータ作成やスライス設定を行うことでより効果的に3Dプリンタを活用できるようになります。