【事例紹介】73年続く超至近距離のものづくりをデジタル技術でより多く、より広い範囲の人へ届ける|株式会社徳田義肢製作所
- Yokoito PR
- 1月30日
- 読了時間: 8分
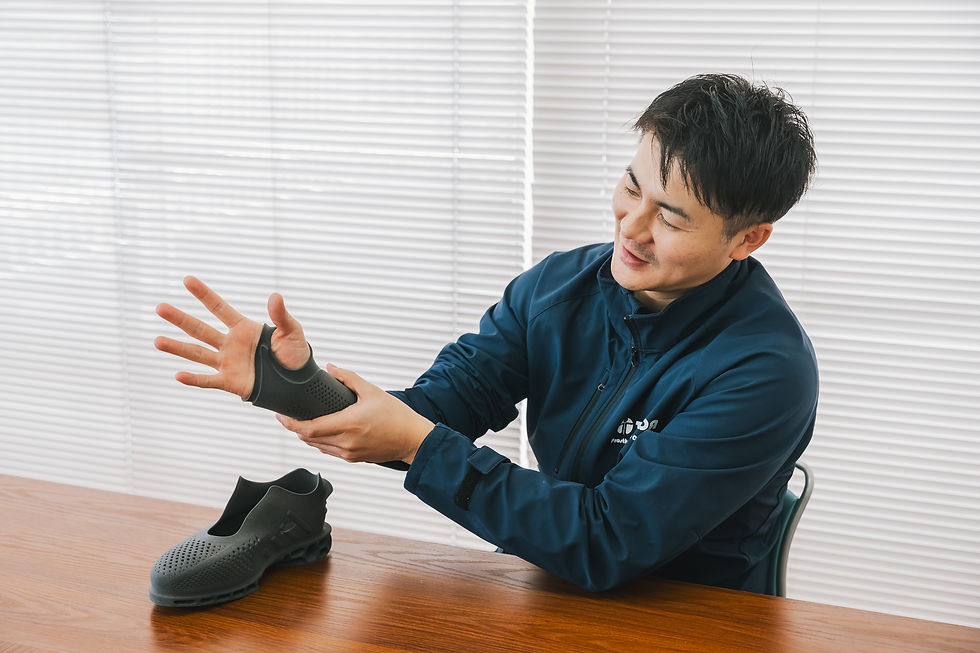
Yokoito Additive Manufacturing(YAM)で導入支援をしたSLS方式3Dプリンター「Fuse 1」および「Fuse 1+」を活用した事例として、株式会社徳田義肢製作所(以下、徳田義肢製作所)の取り組みを紹介します。
徳田義肢製作所は熊本県を拠点に、身体活動を支援するオーダーメイド製品を提供する老舗企業です。
手足を切断した方のための義肢や、麻痺や骨折などで生じた機能を補う装具。徳田義肢製作所は、「超至近距離のものづくり」で患者ごとにまったく異なるニーズに応え続けてきました。
大学病院や整形外科、リハビリテーション科などで患者一人ひとりに合わせた義肢装具を提供してきた実績だけでなく、研究開発型の姿勢を貫き、新たな技術に果敢に挑み続けています。とくに近年は3Dプリント技術の導入により、これまで作り手の経験と勘に頼ってきた工程をデジタル化することで、製品開発のスピードや品質を飛躍的に高めているそうです。
患者さんが「したいこと」を実現するために、自分たちにできることは何か。
企画室室長を務め、義肢装具士でもある徳田和彦さんに医学と工学の知識を融合させ、従来の枠組みにとらわれずに進化していく同社の取り組みを存分に語っていただきました。
取材ご協力:
株式会社徳田義肢製作所 企画室室長・義肢装具士
徳田 和彦様
超至近距離のオーダーメイドが支える「身体活動」
――まずは御社の事業内容を教えてください。
当社は設立から73年目を迎えます。主に整形外科やリハビリテーション科を中心とした医療機関からの依頼で、義肢装具をつくる会社です。たとえば、切断された手足の代わりにつける「義肢(義足・義手)」や、脳卒中や事故、脊髄損傷などで麻痺した手足に機能を補う「装具」の製作を手がけています。
一口に「義肢・装具」と言っても、患者さんの年齢や性別、生活環境、就労状況から収入環境まで、一人ひとりが求める機能や形状はまったく異なります。そこで大切なのが「超至近距離」のものづくりです。患者さんとの距離を極力近づけ、実際に何を望んでいるのかを細かくヒアリングし、形状や部品選択をオーダーメイドで決めていくという、とても特殊な業務形態になっています。

徳田義肢製作所本社(熊本県熊本市)
医学と工学の融合で培ってきた研究開発力
――徳田義肢製作所の強みや、長く続けてこられた理由はどこにあると感じますか?
超至近距離でのオーダーメイド製造という長年のノウハウ、そして医学と工学をマッチングさせる研究開発力だと思います。医療の現場では「こんなものが欲しい」というアイデアはあっても、工学知識がないために実現できないケースがたくさんあります。逆に工学サイドは「こう作れる」けど、医学の考え方を深く理解していないと、求められているものとズレてしまう。
当社は義肢装具士という国家資格を持った臨床家が中心にいて、製造技術を長年培ってきた熟練の技術者とのチームワークもあります。そこに研究開発の要素を加えて、蓄積されたノウハウを応用・転用しながら新しいものを生み出す。そういった流れを続けてきたことで、変化の激しい社会や医療のニーズにも柔軟に対応できる体制が築けているのかなと思います。
Fuse導入の決め手と得られたインパクトとは
――続いて、3Dプリンター(Formlabs Fuse シリーズ)の導入背景と経緯を教えてください。
もともと2014年から3Dプリンティングの研究は行っていました。というのも、試作品を外注で削り出してもらうと費用が非常に高く、試作と検証を繰り返すスピードも遅い。そこで自社に安価なFDM方式の3Dプリンターを導入し、形状確認や組み立て機能のチェックを始めたんです。
ただ、FDMだと最終製品として患者さんに渡せるほどの強度や寸法精度は得られませんでした。体に直接装着して毎日使うものですから、破損や事故が起きると非常に危険です。さらに、材料の選択肢が限られていて、医療現場で求めるような信頼性を確保するのは難しかった。そこで「いつかは粉末焼結方式(SLS)やMulti Jet Fusion(MJF)に行き着くだろう」と思いながら、市場をウォッチし続けていました。
ちょうどそのとき、FormlabsのFuse 1に出会ったんです。MJFのように数千万円単位の投資をするよりも導入コストが抑えられ、かつ表面の仕上がりや寸法精度も高い。サイズ感はやや小さいものの、まずは義足パーツや小さい装具部品をつくるには十分でした。そこで補助金も活用しながらFuse 1を導入し、試作だけでなく最終製品にも徐々に応用していったんです。
Fuse設置場所の様子
スポーツ用義足カバーの事例

――具体的に3Dプリンターを使った製品として、どのようなものがありますか?
たとえば「スポーツ用義足のカバー」は一つの成功事例ですね。体育館の床って金属の義足が直接ぶつかると傷がつくことが多いんです。また、義足側にダメージが加わることもある。そこで従来は布をかぶせたり、簡易的なカバーを装着したりしていましたが、動きづらかったり外れやすかったりするデメリットがありました。
そこで3Dスキャンを活用し、実際の義足にピタッとはまるように設計したカバーをFuseシリーズ(SLS方式)で造形したんです。材料はTPU(熱可塑性ポリウレタン)を選び、表面は柔らかいけど強度も確保できるよう、パラメーターを細かく調整しました。ワンタッチで装着できて、動きも損なわれない。実際に体育館で使ってみても床へのダメージがほぼなく、ユーザーさんからも「すごく動きやすいし、見た目がかっこいい」と好評でした。
開発された製品
デジタル化がもたらすこととは

――3Dスキャンや3Dプリントなどのデジタル技術がもたらす大きな利点は何でしょう?
やはり「自動化」と「均質化」の恩恵が大きいです。義肢装具は個人の経験や勘に左右される部分が多く、同じものを作るにしてもベテランと新人で仕上がりの質が変わるリスクがあります。ところが、デジタルでスキャンしてCAD上で形状をモデリングすれば、ある程度の品質を機械に任せられる。結果として患者さんへの提供品質が安定しやすくなるんです。
さらに、3Dプリンターは深夜や休日でも作業してくれますよね。オーダーメイドなので「金型を作って大量生産してコストを下げる」というアプローチが取りづらい。しかし、SLS方式で複数モデルをまとめて成形できる点は非常に大きいと思います。これが経営的視点で言う「働き方改革」の実現にも直結します。
義肢装具は使用者の体の一部になりますから、定期的な調整や修理が発生し得るんです。でも技術者が休んでいても、クラウド経由で作りたいデータがあればプリンターが動いてくれる。生産性を確保しやすいのは大きな武器です。私たちのような中小企業でも人員の負担を減らしつつ、高品質なものを作り続けられる可能性が出てきました。
徳田義肢製作所のこれから
――医学と工学の融合という意味では、制度面での遅れもあるのでしょうか?
そうですね。3Dプリンターで作られた装具は、まだ正式に保険適用などで認められていない部分が多いです。技術のほうが先に進んでいて、制度が後から追いかける形。厚生労働省や学会も現状を把握し始め、動きはありますが、これから本格的に整備される段階だと思います。
ただ、このハードルがクリアできれば、義肢装具業界全体で3Dプリンティングが普及していく可能性は大いにあります。そのときに備えて、私たちはすでにいろいろな応用事例を積み上げておきたいんです。研究開発で得られた成果やノウハウを業界に先駆けて蓄積し、患者さんにとってより良い製品を届けられるようにしておく。そこが今、一番力を入れている部分ですね。

――今後、事業をさらに広げる上での構想などはありますか?
義肢装具は一人ひとりと対面でやりとりをしていく必要があるので、どうしても地理的な制限が出てしまいます。しかしせっかく持っている技術を、熊本や近隣県だけで終わらせてしまうのはもったいない。そこで、全国各地へビジネスを展開できるよう株式会社トクダ オルソ テックというBtoB領域の会社をつくったり、すでにデジタルスキャンから製造まで、一気通貫でデータ処理できるシステムは完成したので、遠隔地の患者さんがデータを送ってきて、うちで製造・調整して送り返すシステムの構築を目指しています。
たとえば患者さんの足型を3Dスキャンしてデータ化すれば、スキャンデータをクラウド上にアップロードしてもらい、うちで製造して届けることができますよね。これまで技術者が直接出向かないと作れなかった装具を、より広範囲へ届けられるようになるわけです。こうしてBtoCだけでなくBtoB向けにも技術を提供し、さらに研究開発で生み出した成果を全国に活かす形を整えています。こうした発想は全て、超至近距離で培った「患者さんのためのものづくり」が原点にあります。
ーーありがとうございました!
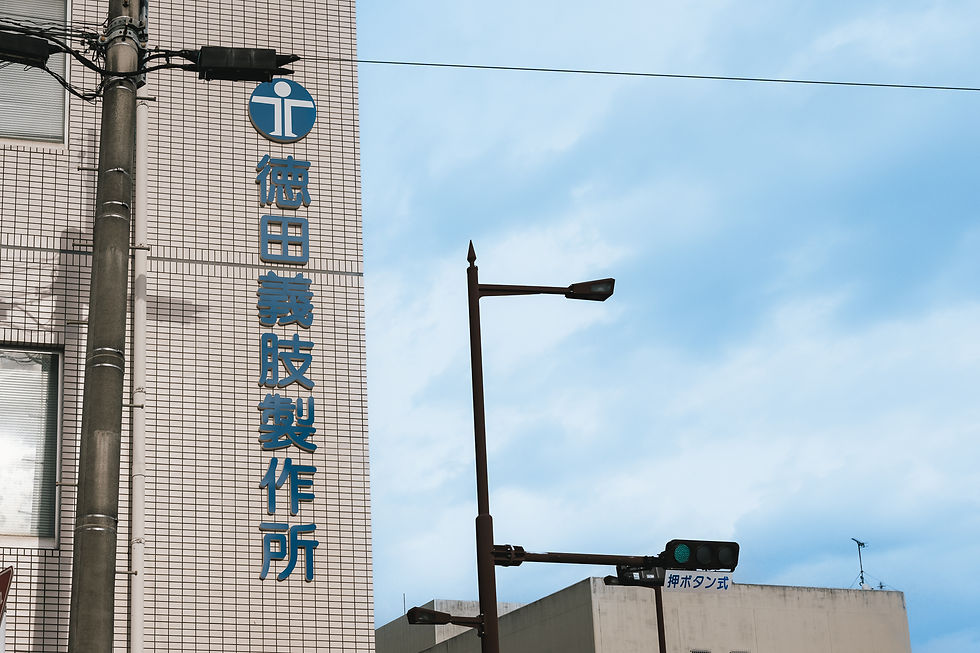
73年という長い歴史の中で、徳田義肢は「医学×工学」を追求し、一人ひとりの患者に寄り添うものづくりをしてきました。そこに、Fuseをはじめとしたデジタル技術を積極的に取り入れる姿勢が加わり、「超至近距離のオーダーメイド×デジタル化」という形で新境地を切り拓いていることが分かりました。
使用者にとって、義肢や装具は身体の一部と言っても過言ではありません。だからこそ、開発スピードや機能性、快適性へのニーズは高い領域だといえます。デジタル活用が本格化し、3Dプリントによる義肢装具が制度面でも認められるようになれば、従来なら想像もできなかったものが生まれるかもしれません。
徳田義肢製作所の今後にこれからも注目し続けたいです。
<本件に関するお問い合わせ>
平日 10:30-13:00・14:00-17:00
Mail: pr@yokoitokyoto.com
Comentarios